THE GREAT ENABLER: PLCS AND THE INDUSTRIAL IOT
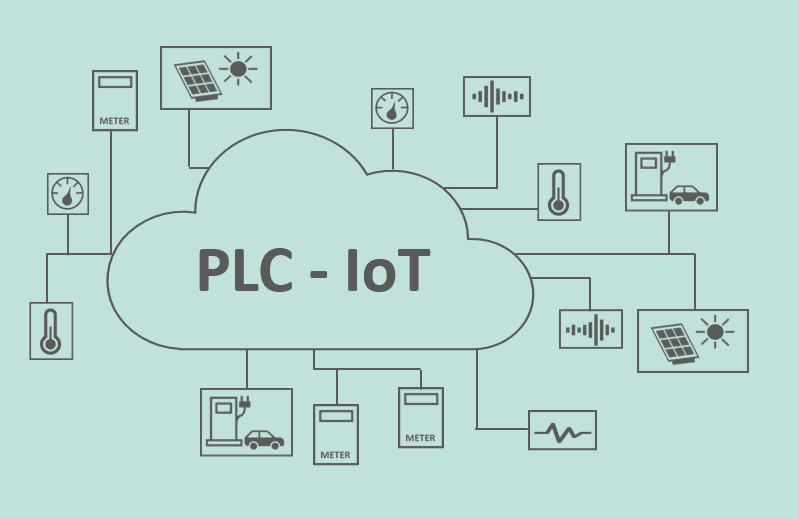
The Industrial market is becoming highly complex, and technology is an enabler. It’s an agent that enables us to gather and understand information in new ways. It drives us to settle down on better choices about how we maintain the organization. Take an example of IOT for instance, in less than a century we've seen industry change through the third modern revolution. The most recent movement, Industry 4.0, presented the possibility of smart factory. Presently we're achieving the tipping point where innovation is developed enough to make that vision occur on a worldwide scale.
The success of Industry 4.0 requires a large number of channels of information to be effectively gathered into the Cloud - stored, organized, grouped and dissected, and at last transformed into enhanced instructions to be communicated to machines, and data to make smart business choices. The outline of hardware, control frameworks, and industrial facility correspondence systems is relied upon to change essentially, which could represent a risk to dominated data collection and control task in traditional automation framework, for example, programmable logic controllers (PLCs) that have until now commanded information accumulation, handling and control undertakings in regular automation framework.
The desire to gather more information to enhance manufacturing yield and assist business decision did not begin with Industry 4.0. Ventures have been hoping to gather expanding amounts of information from equipment and automate exchanges between industrial facility floor and back office expository frameworks before the Cloud. The Industrial PC (IPC) is one case of an idea that rose to empower PC-based automation with the advantages of a consistent information stream to and from chiefs on the corporate LAN. The PLC, be that as it may, holds a few points of interest including long lifecycles and high unwavering quality, and has additionally developed to address and showcase issues by expanding processing capability , providing additional functionality , and incorporation of PC-based standards.
In the event during which PLCs were near, we had to relay, clocks, and electric circle controllers. Process control frameworks were distributed majorly and hardwired into the factory. It was a tedious task to check these frameworks and frequently expect professionals to stroll around the industrial facility throughout the day. As you can envision, this made blame finding exceptionally troublesome. Unmistakably a major issue of these organizations was that downtime could cost a huge number of dollars. This prodded a developing interest for incorporated control. Subsequently, engineers started searching for a dependable substitute to relay logic. Out of this developed, programmable rationale controllers, or PLCs.
PLCs used to be emerging to the point that organizations would introduce PLCs in focal control rooms because of their size and environmental prerequisites. They were remotely wired to handle gadgets using huge measures of cable. Indeed, even with all the extra cost, PLCs had an enormous effect. Flaws were less demanding to discover, downtime lessened, throughput increased and safety improved. At last, it came down to making a business more beneficial, and the PLC emerging to have a high impact.
Stay updated :
Participate on our social stream.